Niente più scuse per non simulare l’intero processo di pressocolata
Il software premium di NovaCast per la simulazione del processo di colata, NovaFlow&Solid, apre sempre a nuove possibilità nel campo della simulazione della pressofusione. Tenendo in piena considerazione anche la prima fase, non ci sono più scuse per non eseguire una simulazione di pressocolata completa prima della produzione dell’attrezzatura. Questo articolo descrive gli sviluppi del software che miglioreranno il lavoro di simulazione. Rendendo più facile ottimizzare il riempimento del getto, progettare l’intero sistema e creare getti pressocolati il più possibile privi di difetti.
Riempimento della camera d’iniezione – tenendo conto di tutta la prima fase di riempimento
Sappiamo che le fonderie, storicamente, adottano per la simulazione temperature di colata troppo elevate. Molte fonderie pensano che ci sia un calo di temperatura molto basso (ca. 20°C) tra il forno fusorio e il riempimento dello stampo. Se la temperatura del forno fusorio è di 700°C, abbiamo scoperto (da prove effettive con termocoppie nella camera d’iniezione) che la differenza di temperatura tra il forno e l’uscita del riempimento della camera (dove inizia il sistema di attacchi di colata) supera i 100°C. La stessa perdita di temperatura è mostrata anche nella simulazione.
Ciò è stato provato in diversi test indipendenti tra loro, tra cui test effettuati all’interno di un progetto condotto dall’Associazione Svedese di Fonderia. In effetti, abbiamo appreso della discrepanza nella perdita di temperatura quando abbiamo avuto la possibilità di simulare la prima fase di riempimento della pressofusione. Abbiamo quindi scoperto di avere un enorme calo di temperatura di cui non avevamo tenuto conto. Con le nuove potenzialità del software, possiamo ottenere le temperature corrette e simulare l’intero processo. L’esecuzione della simulazione completa fornisce impostazioni più corrette per le diverse fasi, mediante il movimento millimetrico del pistone nella camera d’iniezione. È possibile testare diversi punti di inizio della seconda fase, per verificare quando sia meglio avviarla. È inoltre possibile considerare l’aria all’interno della camera, che potrebbe essere inglobata nella fusione durante il riempimento della prima fase, il che aiuterà ad evitare porosità causate dai gas.
La funzione Multi-Mesh velocizza la simulazione della camera d’iniezione del 1000% nella prima fase di riempimento
Mesh con dimensione di cella di 6mm in questa fase di riempimento, per poi passare a 4mm
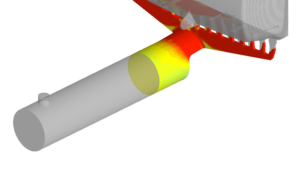
In questa fase la dimensione della cella passa a 2mm per il resto del riempimento
Quando abbiamo simulato per la prima volta l’intero riempimento della camera d’iniezione, ci volle più tempo perché molti elementi dovevano essere calcolati. Dovemmo anche adattare la mesh per il riempimento della forma. Per esempio, se il getto ha uno spessore medio di 4mm, la camera deve essere circa 50-120mm di diametro. Ovviamente non è necessario avere la stessa risoluzione della mesh sia per il getto che per la camera, quindi lo abbiamo preso in considerazione. Per questo motivo abbiamo studiato un modo per utilizzare dimensioni diverse della mesh durante i diversi stadi della simulazione. Questo vuol dire che, per esempio, possiamo utilizzare una mesh da 6mm durante il riempimento della camera e fino all’uscita del metallo dalla stessa. Possiamo poi portare la mesh a 4mm e continuare il riempimento fino a raggiungere la cavità del getto. La mesh viene poi portata a 2mm per avere la miglior precisione possibile all’interno della cavità. Infine, per esempio, si può portare la mesh a 1mm per il calcolo della solidificazione.
Il calcolo della solidificazione è molto più veloce della simulazione del riempimento, quindi è possibile diminuire la taglia della mesh. La multi-mesh può essere aumentata e diminuita più di 10 volte durante la simulazione. Con una dimensione della mesh più grossolana, si possono ottenere calcoli più veloci. Un cambio da 2mm a 6mm durante la prima fase può diminuirne significativamente i tempi, quindi ci vorranno solo alcuni minuti. È quindi possibile concentrare gli sforzi ed il proprio tempo solo sulla parte interessante; cioè la qualità della fusione.
Con le simulazioni accelerate, utilizzando il metodo dei volumi finiti (FVM), e con i vantaggi ottenuti utilizzando la Multi-Mesh, si avrà il tempo di calcolare il gas all’interno della forma e considerare la contropressione. Abilitando il calcolo del gas si può:
• Avere una simulazione più accurata del riempimento dello stampo
• Seguire il movimento delle bolle di gas nella cavità
• Predire le porosità provocate dai gas: posizione e dimensione
• Testare varie posizioni di sfiato per rimuovere le porosità del gas
Simulazione di fronti freddi
In NovaFlow&Solid, il calcolo dei fronti liquidi è stato ampiamente migliorato nel corso degli ultimi sette anni. Ciò significa che ora è possibile simulare in modo accurato quanto lentamente si possa riempire e quanto possano essere sottili le sezioni. Il peso di ogni singola fusione è oggigiorno essenziale, poiché la riduzione del peso consente di risparmiare materiale, energia ed anche il nostro fragile ambiente. Con il nostro software, si possono davvero trovare i limiti per diversi materiali e processi e trovare anche soluzioni alternative che estendano questi limiti.
Terza fase: calcolo dei ritiri
Utilizzando il movimento del pistone all’interno della camera d’iniezione, è possibile impostare una curva di pressione per l’ultimo stadio del processo di riempimento. Tale pressione sarà uguale a quella impostata sulla macchina per il terzo stadio di riempimento. Questa funzione rende il processo di alimentazione/porosità più realistico e corretto.
In conclusione, le nuove potenzialità di simulazione del processo di pressocolata con NovaFlow&Solid permettono di simulare l’intero processo senza perdere troppo tempo ad impostare la simulazione ed eseguirla, dedicandolo invece a studiarne i risultati. La velocità consente di aggiungere più dettagli alla simulazione, come il calcolo del gas e il riempimento della prima fase. Naturalmente, questo darà risultati più precisi. La componente più importante di una simulazione è la base del calcolo, cioè la mesh. NovaFlow&Solid può supportare il costante lavoro di riduzione del peso ed ottimizzazione dei parametri di processo, compresa la diminuzione delle temperature di colata, riducendo l’energia necessaria per la produzione. Miglioriamo costantemente i calcoli per permetterti di essere sempre un passo avanti rispetto ai tuoi concorrenti.